A Flash Forward for Manufacturing Technology
SDSU engineers have introduced a breakthrough for a manufacturing technique called sintering.
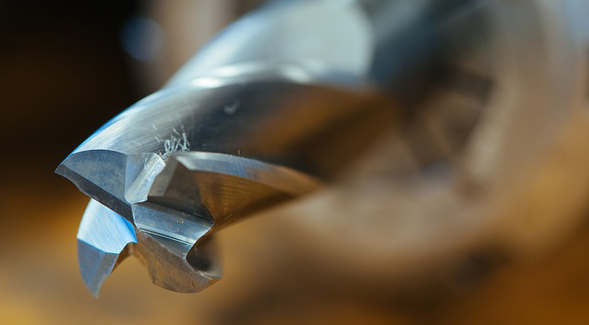
Many materials manufactured today, including ceramics, tungsten carbide and diamond cutting tools, rely upon a technique called sintering. It turns a powdered substance into a solid mass—a process called densification—using heat and pressure. As described in a new study, engineers at San Diego State University have developed a twist on traditional sintering called “flash spark plasma sintering” that can densify materials in a matter of just seconds.“This breakthrough reflects the strength of SDSU engineering programs and in particular in the area of advanced materials research.”
The new process is important because sintering is time- and energy-intensive. Redesigned sintering methods that require less energy and less time, and consequently reduce manufacturing costs, have been a focus of many research efforts over the past several years.
“This newly developed approach dramatically accelerates the time of synthesis, so that it occurs in a ‘flash’—only seconds long—in contrast with regular spark-plasma sintering, which requires minutes, or regular sintering, which requires hours of processing time,” explained the study’s lead author, SDSU mechanical engineering professor and associate dean for research and graduate studies Eugene Olevsky.
Olevsky, along with postdoctoral fellow Charles Manière and Ph.D. student Geuntak Lee, designed the new technique that channels electrical current in narrowly focused areas of the material being sintered. So far, they’ve successfully tested flash spark plasma sintering by densifying samples of powdered nickel, aluminum oxid and zirconium dioxide, but it will work for any other powdered material that can be sintered.
“This technique turns out to be truly all-materials inclusive,” Olevsky said. “We’re able to demonstrate this using these three quite different material systems.”
Introducing controlled electrical fields is a major step forward for sintering technology, which has traditionally just relied upon extreme heat and pressure. The researchers recently described their work with the new technique in journal Nature Scientific Reports.
Manufacturers who produce heavy-duty tools and machine parts out of powdered diamond, tungsten carbine or dozens of other powdered metals, as well as those who use ceramics for industrial uses, will be able to use the new technique to speed up production and save on energy costs, Olevsky said.
The success is a testament to SDSU’s engineering department and specifically its reputation in the world of sintering research. Olevsky’s work in this area, as well as in bioengineering and energy research, will continue inside his lab in the SDSU’s new Engineering and Interdisciplinary Sciences Complex, slated to open in January.
“This breakthrough reflects the strength of SDSU engineering programs and in particular in the area of advanced materials research,” Olevsky said. “SDSU is internationally known as the world center of sintering research.”
Partially adapted from a release written by April Gocha.