Engineers Answer National Challenge, Create Assisted Breathing Device Prototype
Addressing a critical COVID-19 need, an engineering team assembled a prototype from readily available parts. Total cost: $300.
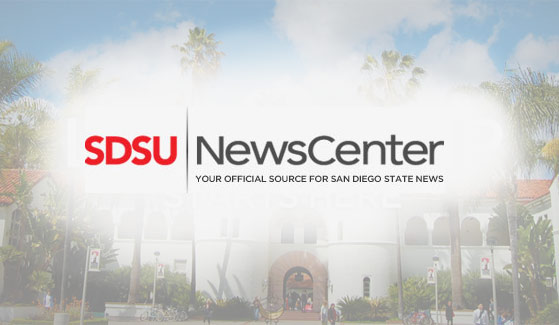
Extreme respiratory distress is one of the complications the coronavirus (COVID-19) produces in very ill patients, when they struggle to breathe on their own and need to be connected to ventilators.
Ventilators are a device of last resort, but with the rapid spread of the virus and the increasing number of critically ill patients, the demand for them is escalating at the same time that hospitals are finding they are in short supply.
When the U.S Department of Defense announced a design challenge in March in response to COVID-19 for easy-to-make, low-cost ventilators, Kevin Wood was one of many researchers who responded.
The assistant professor of mechanical engineering at San Diego State University rallied two of his master’s students, Jack Lucas and Tyler Lestak, and got to work. Their goal: assess what was already out on the market, and design a device that would be affordable but would not require manufacturing of new parts.
What they came up with is a low-cost mechanical assisted breathing device that can be easily assembled using readily available, off-the-shelf parts and common medical supplies.
Initial testing has been completed and the researchers are currently working on further testing with collaborators.
“Professor Wood and his team have shown great ingenuity and passion with their development of this initial prototype,” said Stephen C. Welter, Vice President of Research and Graduate Dean. “We anticipate collaborating with health professionals for further testing and development.”
Only easy to find parts needed
The prototype is based on the resuscitator paramedics use for reviving patients: the bag-valve-mask (BVM) system. The SDSU team’s device is combined with other commonly used components, such as plastic tubing, valves, actuators, which control and move a mechanism, and solenoids — coils of wire used as an electromagnet to convert electrical energy to mechanical energy. It is housed in a simple computer case and the parts cost about $300 when sourced from a local supplier.
Wood, Lucas and Lestak worked with pulmonologists from local hospitals and other medical experts and adapted the design based on input and feedback. Once assembled, the device would just need compressed air and electricity to work.
Wood said being able to make a device that could be assembled quickly without the need for a 3D printer or for the need to manufacture any parts was “its biggest advantage.”
The actuator acts like a plunger that controls the BVM system, sending compressed air in. Knobs on the outside allow medical professionals to adjust the breath volume and speed as well as oxygen flow to the lungs.
The engineers deliberately designed an analog system, in consultation with medical professionals, since digital components could glitch and cause malfunctions.
“We wanted to get the most functionality that we could while keeping it mechanical, since mechanical components last longer than most electrical components,” Wood said.
Initial lab testing indicates that the prototype can hold up for millions of breaths, a critical requirement — typically patients are on ventilators for only a few days. But patients experiencing extreme respiratory distress from COVID-19 may need breathing assistance for weeks.
The system Wood, Lucas and Lestak have developed can deliver mechanically controlled breaths or be used to trigger a patient's breath. The prototype can deliver a respiratory rate between 10 to 40 breaths per minute, and supply a tidal volume (lung volume representing the normal volume of air displaced between breaths) of up to 1,100 milliliters in 0.4 seconds. It is capable of humidifying the air it delivers to help prevent discomfort, and releases expired air through a HEPA filter.
In designing the device, Wood, Lucas and Lestak took into consideration concerns, such as what would happen if a patient coughs, because this would push too much air into the lungs. Current hospital grade ventilators will automatically adjust for such events, which is one reason why they are expensive. For the low-cost assisted breathing device, Wood has built in emergency release valves, which adjust air pressure in these situations to keep the patient's lungs safe.
Another important need for COVID-19 patients is keeping the lungs open at all times by applying a positive pressure to the lungs.
“We can do it in a couple ways that are unique to the system,” Wood said. “One way is to restrict the exhaust so it’s like exhaling through the straw, which keeps the pressure in the patient’s lungs. If the balloon completely deflates, the lung could collapse. Alternatively, we can open the exhaust and push more fresh air and oxygen to the patient’s lungs.”
Next steps for the prototype
From design to working prototype, the device was invented on an accelerated time frame, once the clarion call came from the U.S Department of Defense. It was made possible thanks to collaborations, both on and off campus, representing SDSU’s thriving collaborative research environment.
"SDSU researchers have stepped up at a critical time," said Nick Macchione, San Diego County Director of Health and Human Services Agency. "Professor Wood and his students have put in yeoman efforts and the County appreciates how resourceful and supportive the San Diego research community has been. This type of applied research will help us identify life saving solutions for the future."
To conduct tests, Wood sought the help of his colleague, SDSU researcher Karen May-Newman, whose lab had the instrumentation set up needed to measure air flow and volume. Hala Madanat, director of the SDSU School of Public Health helped connect him with County health officials and potential collaborators for consultations.
Lucas and Lestak, the masters’ students who are graduating this semester, actually put aside their own thesis work to focus on this project.
“Their efforts are nothing short of heroic,” Wood said of his students. With shelter-in-place and physical distancing restrictions, much of the SDSU campus has been open only to critical staff and faculty. So, when Wood initiated this project, College of Engineering Dean Eugene Olevsky designated his work as critical and essential, allowing the team to work in his interfacial design lab.
Wood’s research is focused on lithium-ion batteries, but when he saw the rapidly developing crisis with lack of medical equipment, he felt compelled to do something.
“We have researchers who are showing creativity and initiative in trying to help with the pandemic, with low-cost options,” Welter said. “This skill base is wonderful for the region and the nation to draw upon during these testing times.”
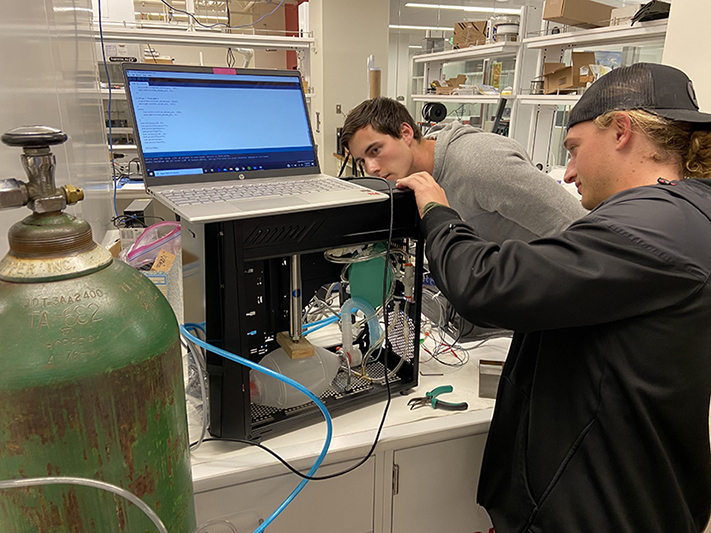
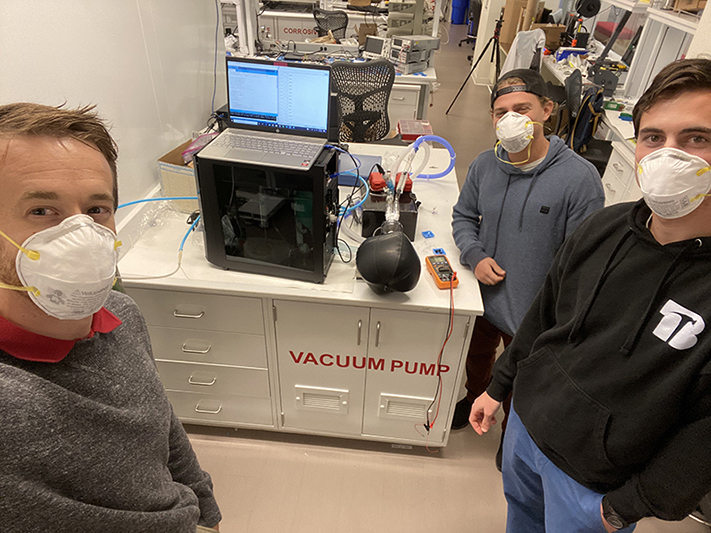
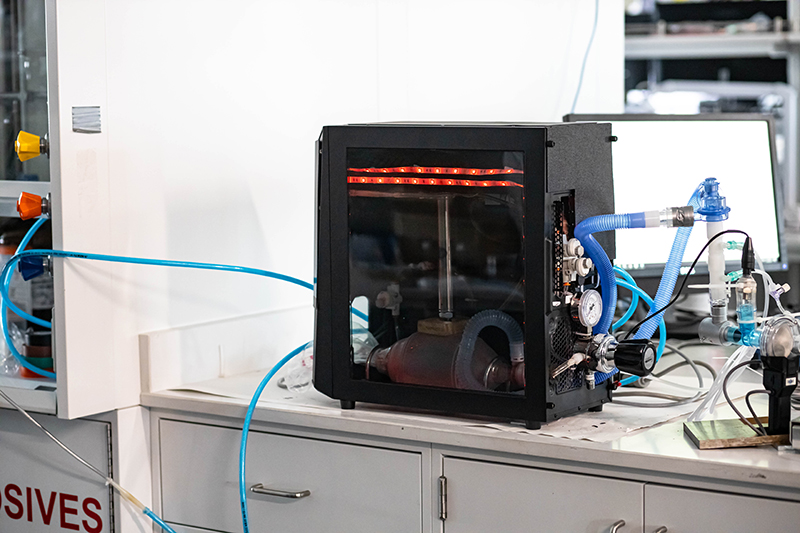
SDSU Engineers Answer the Challenge A mechanical engineering team assembled an assisted breathing device prototype from readily available parts (Photos: Kevin Wood)